Leak Testing of Cooling Jacket by Helium Detecting System
Components employed in the electric powertrains have cooling circuits, either working with refrigerant gas or water glycol mixture, that are needed to remove the heat generated in the normal working conditions. Cooling circuits, cooling plates, hoses and heat exchangers must also be tested for leakage, to guarantee the long-term efficiency of the cooling device or to prevent the leakage of the cooling medium that could lead to a short-circuit.
Marposs can provide a wide range of standard products and customised applications, either manual or fully automated, for the leak testing of the EV components in the complete manufacturing chain.
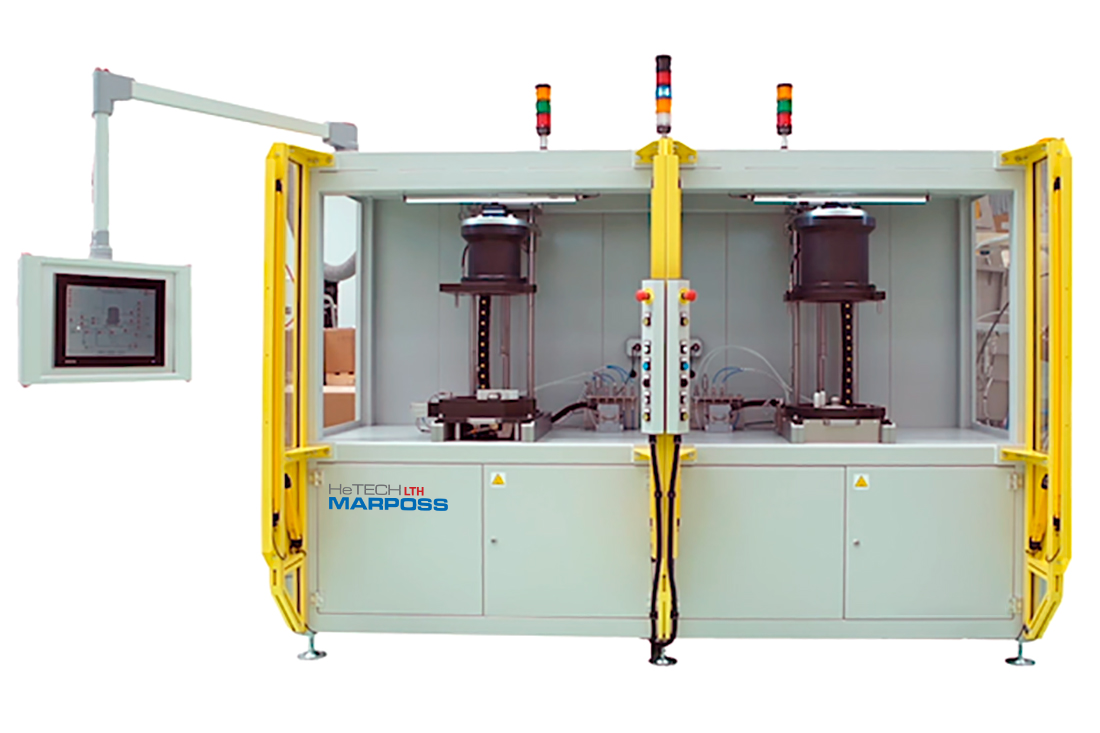
The solution performs a double seal test of the water circuit first and then of the lower flange, for the particular Jacket FRONT and Jacket REAR LONG & SHORT.
It provides nr. 1 “Stand Alone” helium testing plant with two test chambers to check the tightness of nr.2 die-casting jackets for electric motors.
The system includes a vacuum chamber, with automatic opening and closing, positioned on a frame with movable panels in electro-welded and painted steel.
Under the base of the vacuum chamber, the pumping unit is positioned, housed on a support frame inside a soundproof booth equipped with a ventilation system.
On the side of the pump cabin there are the cabinets containing the electrical panel, the analysis system and the pneumatic panel for the process gas distribution.
The man-machine interface consists of a 15" color touch-screen monitor and a push-button panel with controls and indicator lights for the operator at the side of each room.
The jacket to be tested is positioned by the operator or by the robot on the base of the vacuum chamber. The vacuum chamber closes automatically by descending from above and enclosing the piece under test inside it. The gaskets integrated in the vacuum chamber, seal the base of the jacket and separate three distinct volumes: the water circuit, the internal volume of the jacket, and the lower external volume.
While the internal volume is brought under vacuum, the water circuit and the lower external volume are also evacuated and subsequently pressurized with the tracer gas (10% helium and air mixture) to perform the analysis of micro leaks.
Through the mass spectrometer connected inside the jacket, the system is able to detect the loss of the component under analysis, measuring it. Upon successful test, both circuits are discharged from the tracer gas.
Before the helium test, a search for large leaks is performed by measuring the pressure drop in the two circuits during the evacuation of the jacket's internal volume.
- Specific chamber design for each type of jacket (front and rear)
- Separate test result for cooling channel and lower flange
- Configurable HMI touch screen interface
- Push button panel and light signals for easiness of the operator
- Fixture design suitable for loading/unloading by automatic system
- High accuracy of the system
- Test Pressure: 3÷4 bar abs (adjustable) on cooling channel - 0,5÷1 bar abs (adjustable) on lower flange
- Cycle time: 80 sec
- Reject threshold on cooling channel: range E-3÷E-2 mbar l/s with helium @10%
- Reject threshold on lower flange: range E-1 mbar l/s with helium @10%